Vous êtes-vous déjà demandé pourquoi l'écran tactile de votre smartphone peut détecter avec précision chaque mouvement du bout de vos doigts lorsque vous tapez ? L’un des secrets de cette technologie réside dans la technologie capacitive. La technologie capacitive est utilisée dans les écrans tactiles et trouve de nombreuses applications dans le domaine des capteurs.
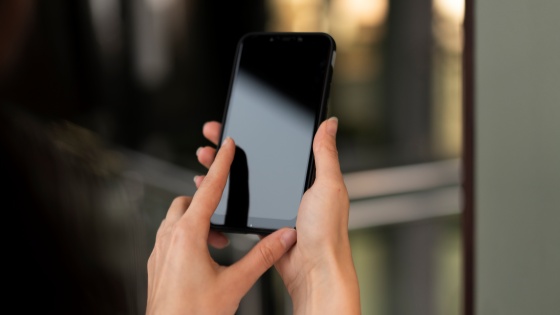
Introduction
Un capteur de pression capacitif est un type de capteur qui mesure la pression en fonction des changements de capacité. Il fonctionne en mesurant le changement de capacité entre deux électrodes d'un condensateur pour détecter les variations de pression. Ces capteurs sont largement utilisés dans les industries de l'automatisation industrielle, des équipements médicaux, de l'automobile et de l'aérospatiale en raison de leur grande précision, sensibilité et fiabilité.
Principe de fonctionnement des capteurs de pression capacitifs
Principe de base du changement de capacité
Un condensateur est constitué de deux électrodes et d'un matériau diélectrique. Lorsque la distance entre les électrodes ou les propriétés du matériau diélectrique changent, la valeur de la capacité change également. Dans les capteurs de pression capacitifs, ce changement reflète directement la variation de pression.
Relation entre capacité et pression
Dans un capteur de pression capacitif, les changements de pression provoquent une variation de la distance entre les électrodes ou une déformation du matériau diélectrique, entraînant une modification de la capacité. Ce changement de capacité est converti en signal électrique via des circuits électroniques, permettant la mesure de la pression. L'ampleur du signal électrique est proportionnelle à la pression appliquée, permettant une réflexion précise des changements de pression.
Structure typique d'un capteur de pression capacitif
Un capteur de pression capacitif typique se compose d'électrodes fixes et mobiles. La pression agit sur l'électrode mobile, provoquant un changement de position et modifiant ainsi la valeur de la capacité. Ce changement de capacité est détecté et converti en une valeur de pression lisible par le circuit électronique. La conception et le choix des matériaux du capteur affectent directement sa précision et sa stabilité, ce qui nécessite un examen attentif pour garantir sa fiabilité et sa précision.
Types de capteurs de pression capacitifs
Capteurs de pression capacitifs différentiels
Les capteurs de pression capacitive différentielle détectent les changements de pression en mesurant la différence de capacité entre deux condensateurs. Cette conception améliore considérablement la sensibilité et la précision du capteur, car elle peut éliminer les interférences liées aux facteurs environnementaux. Les capteurs capacitifs différentiels sont particulièrement adaptés aux mesures de haute précision et de haute stabilité, comme dans les instruments industriels de précision et les équipements de recherche scientifique.
Capteurs de pression capacitifs absolus
Les capteurs de pression capacitive absolue mesurent la valeur de capacité d'un seul condensateur pour mesurer la pression absolue. Ces capteurs fournissent des lectures précises de pression et sont utilisés dans des applications où la connaissance de la pression environnementale absolue est nécessaire, telles que la météorologie, les baromètres et la surveillance de la pression absolue dans le contrôle des processus industriels.
Capteurs de pression capacitive relative
Les capteurs de pression capacitive relative mesurent la valeur de capacité par rapport à une pression de référence, généralement utilisée pour les mesures de variation de pression environnementale. Ces capteurs sont couramment utilisés dans des scénarios nécessitant la surveillance des changements de pression relative, tels que les systèmes de surveillance de l'environnement des bâtiments, les systèmes de climatisation et certains contrôles de processus industriels.
Avantages des capteurs de pression capacitifs
Haute sensibilité et précision
Les capteurs de pression capacitifs ont une très haute sensibilité et peuvent détecter des changements de pression infimes. Leur conception garantit une relation linéaire entre le changement de capacité et le changement de pression, fournissant ainsi des résultats de mesure très précis. Cette caractéristique les rend adaptés aux applications nécessitant une précision extrême, telles que les dispositifs médicaux et les instruments de mesure de précision.
Faible consommation d'énergie et longue durée de vie
Les capteurs de pression capacitifs se caractérisent par une faible consommation d'énergie, ce qui les rend idéaux pour les appareils nécessitant un fonctionnement à long terme. Leur structure relativement simple, souvent constituée de matériaux durables, garantit une fiabilité et une longévité élevées. Par conséquent, ces capteurs sont largement utilisés dans les applications industrielles et les systèmes de surveillance à long terme.
Adaptabilité à une large plage de températures
Les capteurs de pression capacitifs peuvent fonctionner de manière stable sur une large plage de températures, ce qui les rend adaptés aux environnements difficiles. Les capteurs de pression capacitifs offrent des performances fiables dans les applications industrielles à haute température ou dans des conditions de recherche scientifique à basse température. Cette adaptabilité les rend très appréciés dans l'aérospatiale, l'automobile et d'autres domaines nécessitant un fonctionnement à des températures extrêmes.
En combinant ces avantages et divers types, les capteurs de pression capacitifs jouent un rôle crucial dans la technologie moderne, favorisant le développement et le progrès dans de multiples domaines.
Applications des capteurs de pression capacitifs
Applications dans les équipements médicaux
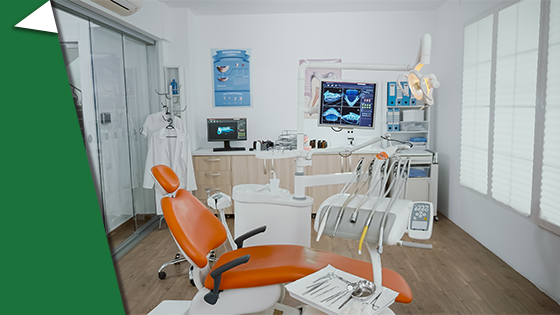
Les capteurs de pression capacitifs jouent un rôle essentiel dans les équipements médicaux. Ils surveillent les indicateurs de santé critiques tels que la pression artérielle et respiratoire, fournissant ainsi des données de santé précises et fiables. Par exemple, les ventilateurs utilisent des capteurs de pression capacitifs pour contrôler avec précision le débit et la pression du gaz, garantissant ainsi aux patients une ventilation appropriée. De plus, les capteurs de pression capacitifs sont utilisés dans divers appareils de diagnostic, tels que les endoscopes et les analyseurs de sang, aidant les médecins à établir des diagnostics et des décisions de traitement précis.
Applications en automatisation industrielle

Dans l'automatisation industrielle, les capteurs de pression capacitifs sont largement utilisés pour surveiller et contrôler la pression dans les processus de production. Ces capteurs peuvent détecter les changements de pression en temps réel, garantissant ainsi la stabilité et la sécurité des processus de production. Par exemple, dans les usines chimiques, des capteurs de pression capacitifs surveillent la pression des réacteurs et des réservoirs de stockage, évitant ainsi les accidents de surpression ou de fuite. Dans la fabrication, ils surveillent la pression des systèmes hydrauliques et pneumatiques, assurant le fonctionnement normal des équipements et la stabilité de la qualité des produits.
Applications dans l'industrie automobile
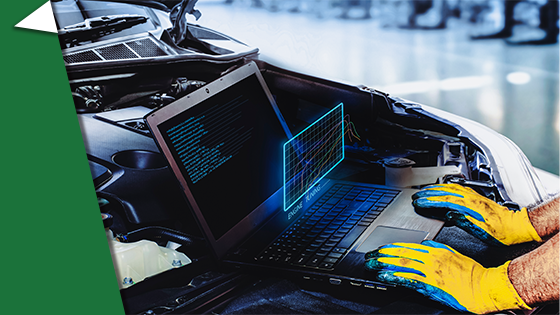
Les capteurs de pression capacitifs ont de nombreuses applications dans l'industrie automobile. Ils sont utilisés dans les systèmes de gestion moteur pour surveiller la pression d'admission et la pression du carburant, optimisant ainsi les performances du moteur et le rendement énergétique. De plus, des capteurs de pression capacitifs sont utilisés dans les systèmes de surveillance de la pression des pneus (TPMS) pour fournir des informations sur la pression des pneus en temps réel, améliorant ainsi la sécurité de conduite. D'autres applications incluent la surveillance de la pression dans les systèmes de freinage, les systèmes de suspension et les airbags, garantissant la stabilité et la sécurité du véhicule dans diverses conditions.
Applications en aérospatiale
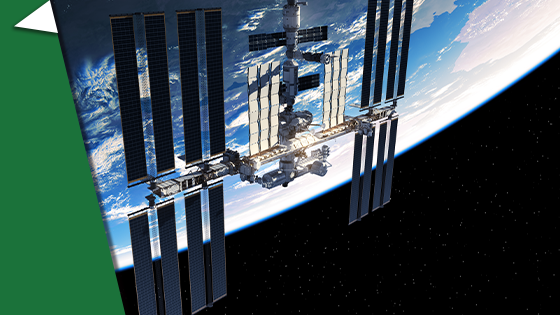
Dans le domaine aérospatial, les capteurs de pression capacitifs mesurent divers paramètres de pression des avions. Ces paramètres incluent la pression de la cabine, la pression du carburant, la pression du système hydraulique, etc., garantissant la sécurité et les performances de l'avion. Par exemple, dans le système hydraulique d'un avion, des capteurs de pression capacitifs surveillent la pression de l'huile hydraulique pour assurer le fonctionnement normal du système de contrôle. Dans les vaisseaux spatiaux, ces capteurs surveillent la pression des systèmes de propulsion et de contrôle environnemental, garantissant ainsi le succès des missions spatiales.
Les capteurs de pression capacitifs, avec leur sensibilité, leur précision, leur faible consommation d'énergie et leur durabilité élevées, sont largement utilisés dans de nombreux domaines, devenant ainsi un élément indispensable de la technologie moderne. En tant que produit de XIDIBEI, leXDB602Le transmetteur de pression industriel à membrane plate en silicium diffusé de la série présente d'excellentes performances et de larges perspectives d'application, jouant un rôle important dans les domaines susmentionnés.

Comparaison des capteurs de pression capacitifs avec d'autres capteurs
Capteurs de pression capacitifs ou résistifs
Les capteurs de pression capacitifs et les capteurs de pression résistifs diffèrent considérablement en termes de principes de fonctionnement et d'applications.
Sensibilité et précision: Les capteurs de pression capacitifs ont généralement une sensibilité et une précision plus élevées car les changements de capacité peuvent refléter avec précision des changements de pression infimes. En revanche, les capteurs de pression résistifs ont une sensibilité et une précision moindres, en particulier dans les plages de basse pression.
Structure et coût: Les capteurs de pression capacitifs ont une structure relativement complexe, nécessitant des processus de fabrication précis, et entraînant des coûts plus élevés. Les capteurs de pression résistifs ont une structure plus simple, des coûts de fabrication inférieurs et conviennent à la production et aux applications de masse.
Scénarios applicables: Les capteurs de pression capacitifs, en raison de leur haute précision, conviennent aux scénarios nécessitant une sensibilité et une précision élevées, tels que les dispositifs médicaux et les mesures industrielles de précision. Les capteurs de pression résistifs sont couramment utilisés dans des applications où la haute précision n'est pas cruciale mais où la durabilité et la rentabilité sont importantes, telles que l'automatisation industrielle générale et l'électronique grand public.
Capteurs de pression capacitifs ou piézoélectriques
Les capteurs de pression capacitifs et les capteurs de pression piézoélectriques présentent des différences distinctes en termes de réponse en fréquence et de scénarios d'application.
Réponse en fréquence: Les capteurs de pression capacitifs conviennent aux mesures de pression basse fréquence, fournissant des données de pression basse fréquence stables et précises. Les capteurs de pression piézoélectriques excellent dans la détection des changements de pression à haute fréquence et dans la réponse rapide aux changements de pression instantanés, ce qui les rend idéaux pour les mesures de pression dynamiques.
Champs d'application: Les capteurs de pression capacitifs sont couramment utilisés dans des scénarios nécessitant une mesure continue et stable, tels que la surveillance du niveau de liquide, la mesure de la pression atmosphérique et la surveillance continue des dispositifs médicaux. Les capteurs de pression piézoélectriques, en raison de leur sensibilité aux vibrations haute fréquence et aux pressions d'impact, sont largement utilisés dans les accéléromètres, la surveillance des vibrations et les tests d'impact.
Avantages et inconvénients: L'avantage des capteurs de pression capacitifs réside dans leur haute sensibilité et leur stabilité, mais leurs performances sont limitées dans les mesures haute fréquence. Les capteurs de pression piézoélectriques excellent dans la réponse haute fréquence mais peuvent connaître une dérive dans les mesures de pression statique à long terme. Par conséquent, chacun a ses avantages et ses inconvénients, et le type de capteur approprié doit être choisi en fonction de l’application spécifique.
Résumé
Les capteurs de pression capacitifs fonctionnent parfaitement en termes de sensibilité, de précision et de mesures basse fréquence, ce qui les rend adaptés aux applications nécessitant une précision et une stabilité élevées. Les capteurs de pression résistifs, avec leur structure simple et leur faible coût, présentent des avantages dans de nombreuses applications. Les capteurs de pression piézoélectriques, en raison de leurs caractéristiques de réponse haute fréquence, fonctionnent bien dans les mesures de pression dynamique. Les utilisateurs doivent sélectionner le type de capteur approprié en fonction de besoins spécifiques et de scénarios d'application pour obtenir les meilleurs résultats de mesure et la meilleure rentabilité.
Tendances de développement futures des capteurs de pression capacitifs
Développement de nouveaux matériaux et technologies
Avec l'avancement continu de nouveaux matériaux et technologies, les performances des capteurs de pression capacitifs seront encore améliorées. À l’avenir, les capteurs utiliseront des matériaux plus avancés, tels que des nanomatériaux et des matériaux intelligents, qui présentent une sensibilité et une durabilité plus élevées. De plus, le développement de la technologie des systèmes microélectromécaniques (MEMS) rendra les capteurs de pression capacitifs plus petits, plus légers et capables d'intégrer davantage de fonctions. Ces avancées technologiques permettront aux capteurs de mieux fonctionner dans des environnements difficiles, élargissant ainsi leur gamme d’applications.
Perspectives d'application futures
Avec le développement rapide de l’automatisation industrielle et des appareils intelligents, les capteurs de pression capacitifs joueront un rôle important dans davantage de domaines. Par exemple, dans les appareils Internet des objets (IoT), les capteurs seront utilisés pour surveiller et contrôler les appareils électroménagers, les infrastructures urbaines et les équipements industriels. Dans le domaine médical, les appareils portables et portables adopteront largement des capteurs de pression capacitifs pour assurer une surveillance de la santé en temps réel. Dans l’industrie automobile, avec la popularisation de la technologie de conduite autonome, les capteurs seront utilisés pour des systèmes plus complexes de surveillance et de contrôle de la pression. Dans l’ensemble, les perspectives des capteurs de pression capacitifs sont très prometteuses, et leur champ d’application devrait encore s’étendre.
Foire aux questions
Quelle est la précision des capteurs de pression capacitifs ?
Les capteurs de pression capacitifs ont une grande précision, capables de détecter des changements de pression infimes. Cela les rend très adaptés aux applications nécessitant des mesures de haute précision, telles que les dispositifs médicaux et les instruments industriels de précision. Leur précision peut généralement atteindre les niveaux du microbar, répondant ainsi à la plupart des besoins de mesure de haute précision.
Pour quels environnements les capteurs de pression capacitifs sont-ils adaptés ?
Les capteurs de pression capacitifs conviennent à divers environnements, notamment ceux présentant des températures élevées, des températures basses et des changements d'humidité importants. Leur conception et leur sélection de matériaux offrent une bonne adaptabilité à l'environnement, leur permettant de travailler de manière stable dans des conditions difficiles. Par exemple, dans l’industrie pétrolière et gazière, les capteurs doivent fonctionner sous des températures et des pressions élevées pendant des périodes prolongées, tandis que dans le domaine aérospatial, les capteurs doivent maintenir leur précision et leur fiabilité dans des conditions extrêmes de température et de pression.
Comment les capteurs de pression capacitifs sont-ils calibrés ?
L'étalonnage des capteurs de pression capacitifs nécessite l'utilisation d'une source de pression standard. Le processus d'étalonnage consiste à connecter la source de pression standard au capteur et à ajuster le signal de sortie du capteur pour qu'il corresponde à la valeur de pression standard. Un étalonnage régulier garantit la précision des mesures du capteur, ce qui est particulièrement important dans les applications de haute précision.
Quelle est la durée de vie des capteurs de pression capacitifs ?
Les capteurs de pression capacitifs ont une longue durée de vie, généralement plusieurs années. Leur durée de vie spécifique dépend de l'environnement d'utilisation et de la fréquence. Avec une utilisation normale et un entretien régulier, les performances du capteur peuvent rester stables pendant longtemps. Par exemple, dans les applications industrielles, les capteurs peuvent devoir résister à des changements de pression continus et à des environnements difficiles, mais avec un entretien approprié, leur durée de vie peut toujours répondre aux attentes.
Quel est le coût des capteurs de pression capacitifs ?
Comparés à d'autres types de capteurs de pression, les capteurs de pression capacitifs ont des coûts plus élevés. Cependant, leur haute précision et leur grande fiabilité valent l’investissement. Bien que l’investissement initial soit plus élevé, leurs faibles besoins de maintenance et leur longue durée de vie peuvent réduire les coûts globaux à long terme. Pour les applications nécessitant une précision et une stabilité élevées, les capteurs de pression capacitifs constituent un choix idéal.
Les capteurs de pression capacitifs doivent-ils être remplacés régulièrement ?
Tant qu'ils sont utilisés normalement et entretenus régulièrement, les capteurs de pression capacitifs n'ont pas besoin d'être remplacés fréquemment. Un étalonnage et une maintenance réguliers garantissent un fonctionnement stable à long terme des capteurs. Dans certaines applications extrêmes, un remplacement peut être nécessaire en fonction de conditions spécifiques, mais dans l'ensemble, les capteurs de pression capacitifs offrent des performances fiables et durables.
Conclusion
Les capteurs de pression capacitifs ont de larges perspectives d’application dans divers domaines, grâce à leur sensibilité, leur précision et leur adaptabilité élevées qui en font un élément indispensable de la technologie moderne. Avec les progrès technologiques continus et l’application de nouveaux matériaux, les capteurs de pression capacitifs continueront à jouer un rôle crucial dans des domaines émergents. En comprenant leurs principes de fonctionnement, leurs avantages, leurs applications et leurs problèmes courants, les utilisateurs peuvent mieux sélectionner et appliquer ces capteurs hautes performances, fournissant ainsi des solutions de mesure de pression fiables pour divers scénarios d'application.
Heure de publication : 18 juin 2024